Приглашаем вас на экскурсию в одно из крупнейших предприятий, находящихся за Уралом – на Новосибирское предприятие ОАО "Завод "Экран", производящее стеклянные изделия. Довольно странное название объясняется тем, что до своего перепрофилирования завод производил телевизионную технику.
А мы расскажем о том, как рождаются стеклянные бутылки и не только.
Здесь производят бутылки из бесцветного стекла ёмкостью от 0,25 до 1 литра для газированных напитков, пива и ликёро-водочных изделий, бутылки из коричневого стекла, а также банки ёмкостью от 0,25 до 3 литров для соусов, соков и других консервированных продуктов.
Стекловарная печь.
Будучи самым крупным производителем стеклотары на территории от Урала до Дальнего Востока, завод выпускает 620 миллионов единиц стеклотары в год (почти 1,7 миллионов единиц в день).
Производство стеклянной тары – это два цеха (для изготовления бесцветных бутылок и коричневых бутылок).
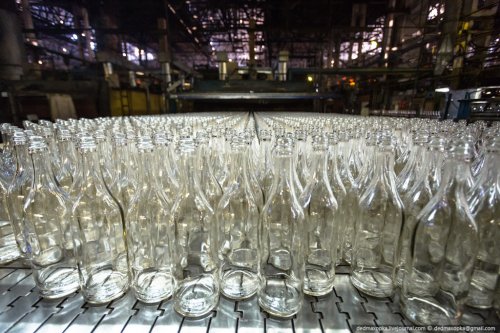
Эти бутылки уже готовы, но ещё не прошли проверку на качество.
Процесс производства стеклянной тары состоит из нескольких последовательных этапов: подготавливается исходное сырье, составляется шихта, затем осуществляется варка стекломассы, формируются и отжигаются изделия, которые на последнем этапе проходят контроль качества и упаковываются.
Исходные сырьевые компоненты очищаются от нежелательных примесей, после чего подготавливаются для дальнейшей обработки и применения. Шихта – это сухая смесь материалов, подаваемая в печь для того, чтобы получить стекломассу. Чтобы получить однородную массу, в процессе составления шихты компоненты взвешиваются в определённых пропорциях и перемешиваются.
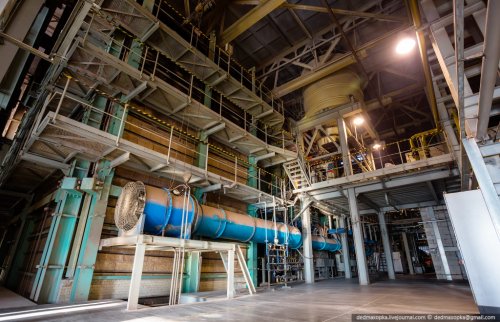
Это – стекловарная печь: в неё подают шихту и стеклобой. Такая печь производит почти 180 тонн стекломассы в сутки.
Варка стекломассы является самой сложной операцией в производстве стеклянной тары. Она осуществляется в ванных печах непрерывного действия, которые представляют собой сложенные из огнеупорных материалов бассейны.
Когда шихта нагревается до температуры 1100-1150ºС, образуются силикаты сначала в твёрдом виде, а затем в расплаве. Дальнейшее повышение температуры в расплаве приводит к полному растворению наиболее тугоплавких компонентов, в результате чего образуется стекломасса, которая является неоднородной по составу и насыщенной газовыми пузырьками. Чтобы её осветлить, температуру повышают до 1500-1600ºС.
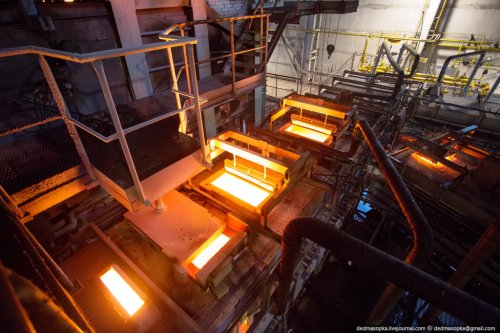
Стекломасса на выходе из стекловарной печи.
Прозрачность и цвет бутылок зависят от добавления (или отсутствия) красителей и глушителей в шихту. Благодаря глушителям (соединениям фосфора, фтора и т.п.) стекло становится непрозрачным. Разный цвет стекломассы достигается с помощью различных соединений: синий цвет – это соединения кобальта, зелёный цвет – хрома, фиолетовый – марганца, сине-зелёный и коричневый – железа и другие.
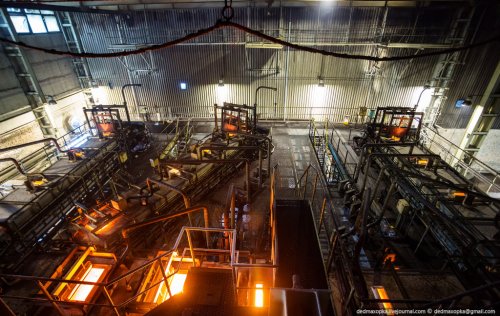
Этот процесс довольно неприятно пахнет.
По окончании стекловарения стекломасса охлаждается до температуры приобретения вязкости, требуемой для выдувания стеклянных форм.
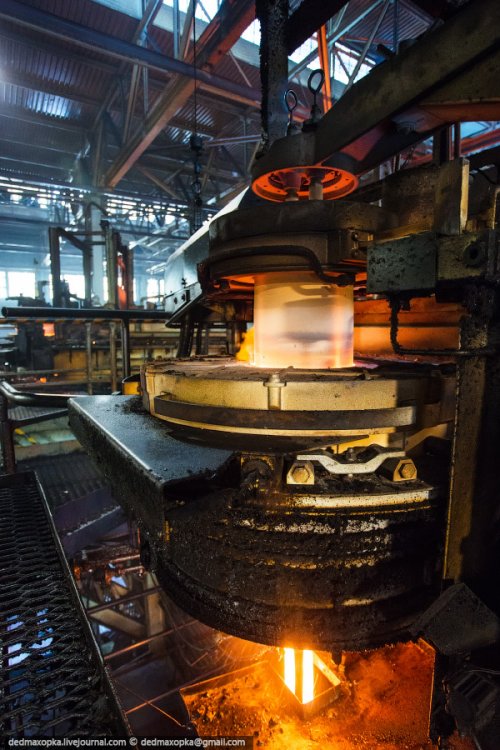
Стекломасса подаётся на стекольные линии. Внизу снимка видно, как падают две яркие капли стекломассы – они в будущем и станут бутылками.
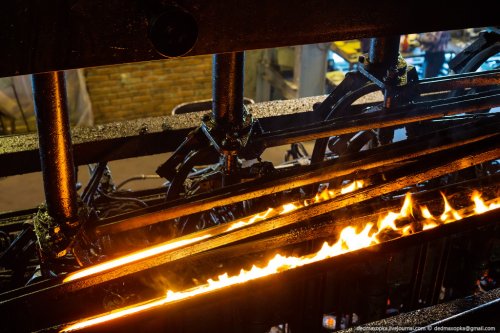
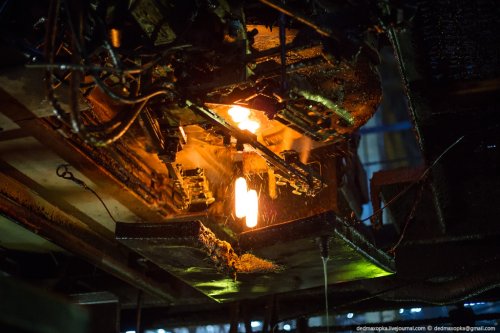
А вот сам процесс создания капель стекломассы.
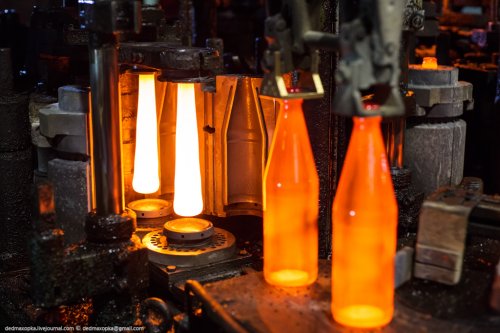
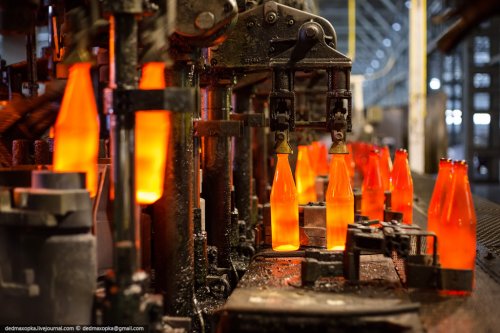
Готовую стекломассу подают к формовочным автоматам, осуществляющим формовку изделий.
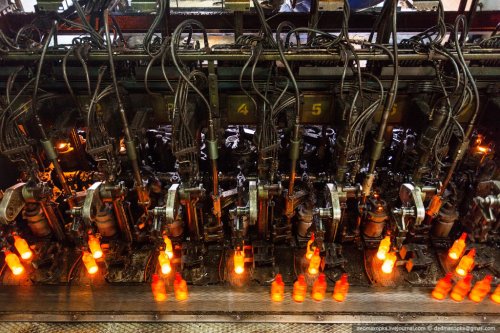
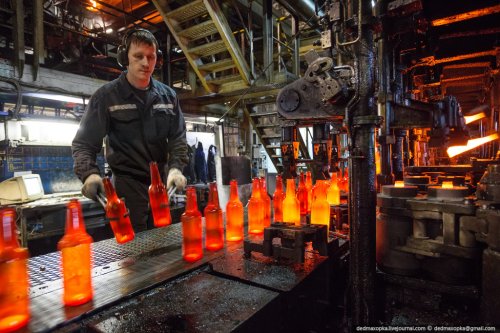
10-тисекционная линия, которая производит бутылки из коричневой стекломассы.
После формовки стеклоизделия подвергаются дополнительной термической обработке (отжигу) в печах прямого нагрева. Благодаря отжигу, в стеклотаре снимается внутреннее остаточное напряжение, обеспечивая изделие сохранностью в процессе дальнейшей обработки и последующей эксплуатации.
На входе в печь отжига изделия имеют температуру около 400-500 градусов Цельсия, а на выходе – около 50-80-ти.
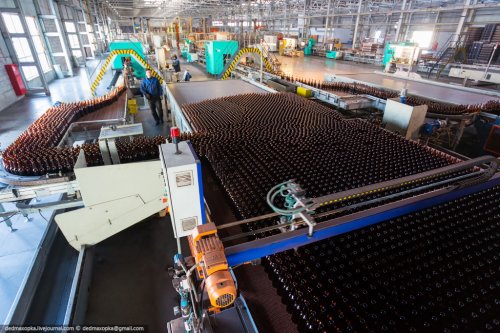
Стеклотара после отжига.
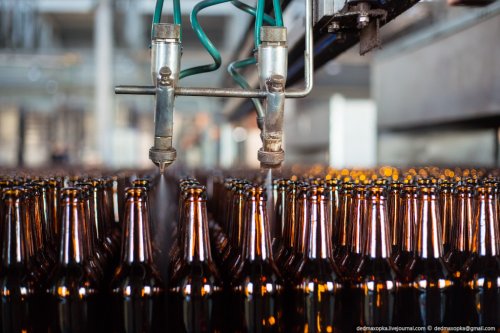
Бутылки опрыскиваются специальным раствором, защищающим их от потёртостей и царапин во время транспортировки.
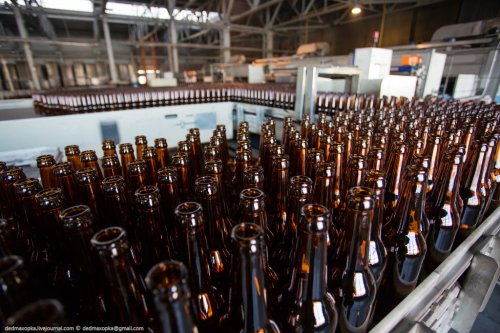
Продукции остаётся пройти контроль качества.
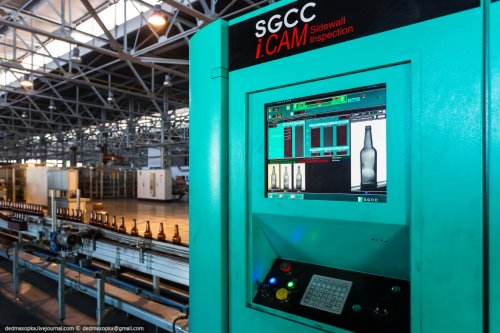
В этом цехе установлены современные инспекционные машины, ежесекундно сканирующие каждую стеклянную бутылку на соответствие установленным требованиям.
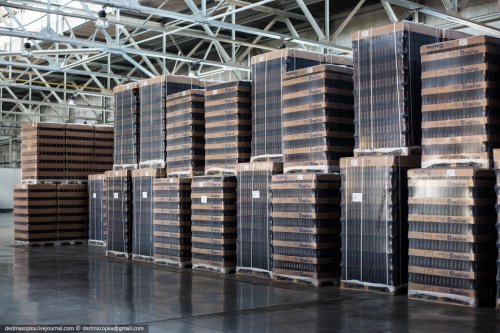
Продукция уже упакована.
В другом цехе производятся прозрачные бутылки и банки, а контроль качества осуществляется вручную.
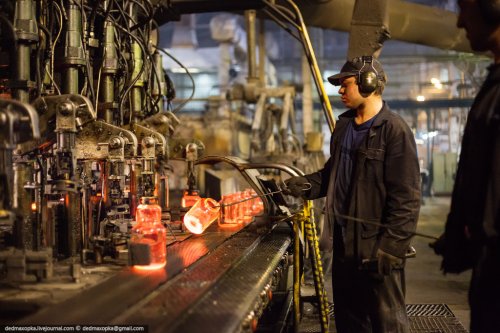
В обоих цехах всегда очень шумно, поэтому все работники ходят в берушах или в шумопоглощающих наушниках.
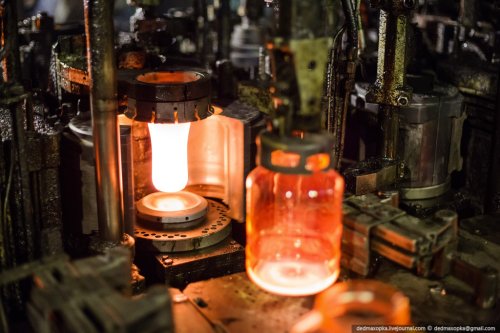
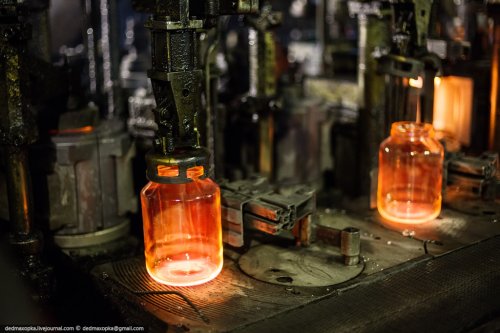
Процесс изготовления 2-литровой банки.
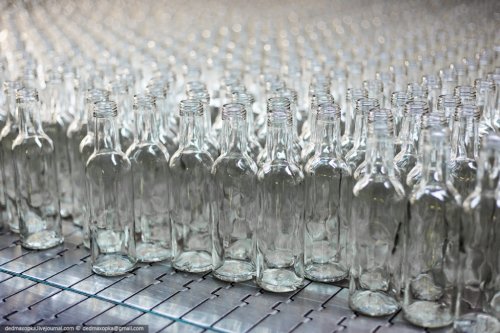
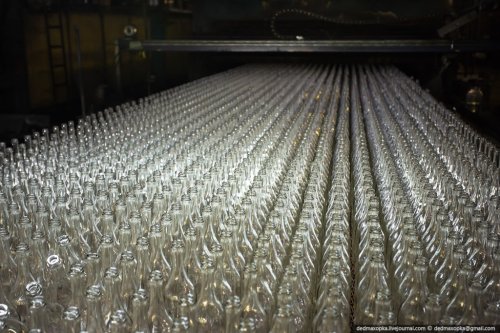
Водочные бутылки после термической обработки.
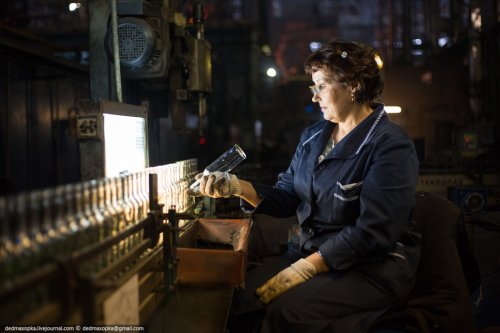
Контроль качества.
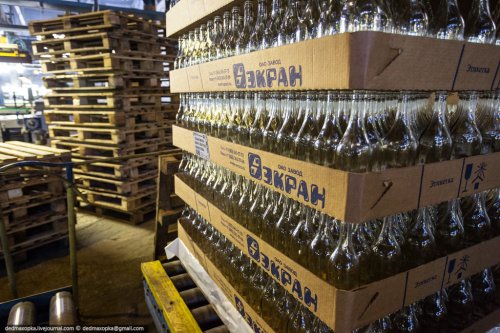
Готовая продукция.